刘厂长是一家中美合资企业的厂长,该企业由中美双方各出资50%,在管理上也是互有分工:刘厂长代表中方负责管理公司的生产,美方经理负责管理公司的财务和市场。 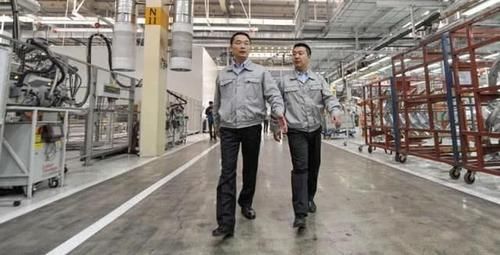
作为一家国内阀门行业的龙头企业,该公司有过自己辉煌的过去。刘厂长深信,即便当时不与美国人合资,自己的工厂照样过得很好。那可真是个惬意的年代,工厂生产什么客户就要什么,即使偶尔有客户提出一些比较特殊的要求,他们也有足够的耐心等,毕竟是特殊产品嘛。 但是,情况逐渐发生了变化。合资后不久,竞争对手如雨后春笋般出现。客户的订单越来越刁钻,什么要求都能提出来。让刘厂长苦恼的是,美方经理似乎完全不理解生产部门的难处——他什么订单都敢接!每当刘厂长提醒美方经理自己的工厂无法这么快完成这么多紧急订单的时候,美方经理总是告诉刘厂长:“刘,我们必须接,否则我们没有足够的订单!”“要你这个做市场的是白吃饭的吗?”刘厂长只能在心里大喊。 对于当前的状况,刘厂长做过基本的分析: 一、生产情况分析说明 第一:阀门生产主要经过A、B、C,D四个车间。100个原材料经过A车间加工后统一送到B车间,然后经过B车间加工后再次以100个为一批 ,搬运到C车间,以此类推,最后变成成品。 第二:从采购原材料到生产出成品,总共需要12天的时间,这12天称之为生产周期。 第三:接到的订单中,大部分要求6天交货,这6天称之为交货期。 问题就在这里了,公司的生产周期远远大于客户对交货期的要求。 刘厂长紧皱着双眉,解决办法是有的,只是……,他似已经可以预知美方经理会做出什么反应。 刘厂长抛出了自己制定的解决方案。 
二、刘厂长的解决方案 方案一:增加库存 制造成品库存 制造标准件库存 方案二:提高产能 “方案一”说明:建立成品库存可以说是刘厂长本能的选择。如果工厂有充足的成品库存的话,那么客户就可以随时取货了。然而,越来越多的客户开始要求定做产品,每个客户的要求又都是不一样的。这样的话,工厂事先根本不知道顾客需要什么产品,那么成品库存也就无从做起了。 因此刘厂长考虑采用增加“标准件”库存的方法。 所谓标准件,是指有一些物料具有通用性,既可以用于产品A,也可以用于产品B,这种具有通用性的物料称之为“标准件”。 原材料经过B车问加工以后成为“标准件”,刘厂长希望在这里增加一定数量的标准件库存。从标准件库存开始到变为成品,需要5天的时间。这样的话,也可以满足客户6天交货的要求。 “方案二”说明:增加产能也是一种可供选择的方法。很多人和刘厂长一样,认为既然产品总是生产不出来,那么我们就不断增加人力、增加设备,通过提升产能来缩短生产周期。当然,最好是深挖内部潜力,争取少花钱就达到增加产能的目的。 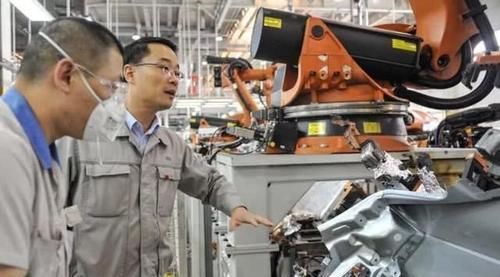
三、美方经理的意见 针对方案一,美方经理坚决不同意。理由: 第一,库存意味着巨大的风险 无论是成品库存还是标准件库存。根据预测制作出来的库存产品有没有人购买呢?因此这是一个巨大的风险。 第二,库存意味着占用大量的资金 在企业利润没有增加的情况下,投入的资金却因为库存而增加,这必然使投资收益率降低。对于一家上市公司来说,这个结果是灾难性的,几乎会立刻招致股价的下跌。 针对方案二,美方经理更是不同意。理由:公司的销售情况不佳,在销售没有增加的情况下却要增加投入,提高产出,显然是不合理的。美方经理在现场观察到,员工与机器设备不是忙不过来,而是有时候忙,有时候闲着没事做。 美方经理的要求: 美方经理认为,现在公司效益严重下滑,而这主要是成本过高造成的。在这种情况下,公司要不断降低成本。因此,美方经理与刘厂长针锋相对的提出,当务之急是压缩库存! 对此,刘厂长被气得七窍生烟!为了借助外力来说服美国人,特意请来了企业管理咨询公司的精益生产专家进行调研,并把自己的想法和盘托出,希望获得精益专家的支持。 在公司上层矛盾重重的情况下是无法开展工作的。因此,必须首先把刘厂长和美方经理的意见统一起来,并且找到双方冲突的根源加以解决。精益生产专家分析说:无论是美方经理还是刘厂长,双方的总目标都是实现企业盈利,这是一个大前提。离开了这个前提,双方就完全没有办法坐到一起解决问题了。美方经理认为,企业要盈利就要压缩生产成本,而压缩生产成本的重要途径,就是削减库存;刘厂长认为,企业要盈利就要保证销售额。在顾客交期的压力之下,缩短交货期就是当务之急。而缩短交货期就要增加库存。同样是为了实现企业盈利,一方要增加库存,一方要削减库存,矛盾冲突相当明显。那么,有没有方法解决这一困局呢? 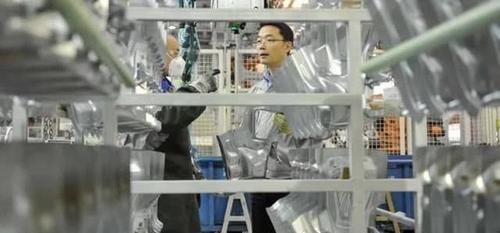
四、精益生产专家给出的解决方案 专家指出,可以同时实现降低库存和缩短生产周期! 缩短交货期的途径不仅限于增加库存,缩短生产周期是另外一条途径。该公司现有生产模式存在巨大缺陷,这个缺陷就是生产与转移的批量过大。例如,A车间生产出来的产品,并不是立刻送到B车间,这个产品必须等待,直到凑足了一个批量才一起搬运到B车间。这就耽误了大量的生产时间。如果能够达到每生产一个产品就立刻送到下工序,则生产周期会极大地缩短。 比如,现有生产模式下,每道工序的生产能力是每分钟加工一个产品,客户订单为100个产品。当一个产品被A工序加工后是不是马上转移到B工序了呢?不是,这个产品必须要等待99分钟,等其他99个产品也加工完毕后才一起转移到B工序。因此,100个原料经过A工序需要100分钟。依此类推,从原材料到成品,一共需要400分钟的时间。而在理想生产模式下,第一个原料经过A工序以后没有等待,直接就开始在B工序上加工。这样的话,4分钟以后,第一个产品就生产出来了,在其后的时间里,每隔1分钟就有一个产品被生产出来,因此,99分钟后,最后第100个产品也已经生产完毕了。于是,生产这100个产品,总共用去了103分钟。 这就是精益生产的基本原理之一:在制品库存越少,生产周期就越短;而生产周期越短,交货周期就越有可能缩短。 对于这种所谓的理想生产模式,刘厂长有似曾相识的感觉。只是,这种模式能成功吗?刘厂长将信将疑。 公司内最近的生产模式也在发生改变,常常出现紧急订单冲击批量转移的情况。在被顾客逼急了的情况之下,跟单员拼命催促生产单位.哪怕只加工出来少量的产品,也被迅速地转移到下一个工序。因此可以说,公司现存两种生产模式,一种是常规的批量转移模式,另外一种则是精益专家的所谓“理想模式”,只是,这种理想模式在工厂内一般是作为应急方法来看待的,一旦顾客放松了交期方面的要求,工厂生产就立刻又转回了“正轨”,一下子又恢复了批量转移的常态。 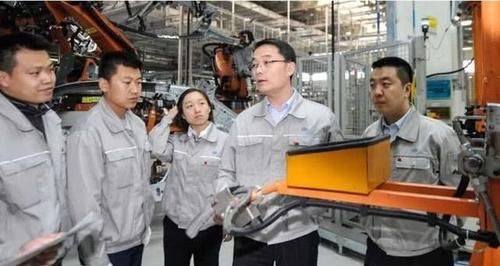
五、新型生产模式 实施精益生产,可以首先建立一条这种新型生产线,然后总结经验,把这种新的生产线推广到全厂。这种新的生产线,称之为“单元生产线”,美国人称之为“workcell”。 单元生产主要从三个方面来实施: 第一,布局。把所有能够放置到一起的机器设备、人员、加工工具按照工艺顺序流水化布局。 第二,多能化培训。通过教育培训,使得一位作业员能够掌握多项技能,每位作业员都能够从头到尾的把一个产品生产完成。 第三,在制品最少。减少中间在制品,消灭周转库存。 改善前:本工序与下工序间距离很远;人员技能单一;生产出一整车的在制品后才推送到下工序。 改善后:大部分工序在布局上连接到了一起;每位作业员都掌握多种技能,能够独立完成整个产品的作业;每加工出一个产品以后,该产品立刻转入下一道工序加工。 六、改善成果 通过实行精益生产,工厂取得了很好的成绩:生产周期缩短了58.33%;在制品库存减少了82.11%;另外,由于在改善过程中大量采用了IE方法,使得人员的生产效率提高了32.39%。从交期角度来讲,顾客要求6天交货,而工厂现在5天就能够把货物生产出来,因此客户的要求得到了满足;从财务角度讲,大量削减在制品库存,使得库存占用的资金获得解放,从而大幅地改善了公司的财务状况。 整个项目,无论是刘厂长还是美方经理都非常满意,认为终于找到了解决问题的根本之道。公司领导坚定信心,从此以后,该公司走上了精益生产之路!
|