0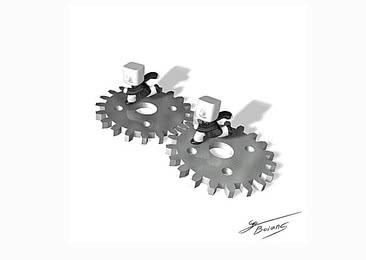
精益生产按需拉动生产运作的方式,关键的一点是其各供应商能实现“精益”供货,即按需要小批量及时供货。要使整个交错并行的供应链实现“精益”,其过程可想而知是非常漫长的。不管企业的精益生产改造进行的深度如何,只要存在采购周期长的原材料/零部件,他们还是得依赖基于“推进式”的MRP进行物料需求计划运算,计算出合理的采购提前期和采购量,以保证生产的正常运作自所以对于踏上精益之路的企业,如何能搭起“精益”与MRP之间的桥梁非常重要。
1.MRP与看板管理之间的差异
(1)主生产计划:MRP系统可以帮助企业将经营规划和生产规划分解为具体的主生产计划,利用MRP提供的模拟功能还可以预计主生产计划改变的影响。看板管理的理论中不涉及如何编制和维护主生产计划,它是以一个现成的主生产计划作为开端的。所以采用准时化生产方式的企业需要依靠其他系统来制定主生产计划。
(2)物料需求计划:MRP可以按照主生产计划、物料清单和库存数据准确地计算出物料需求计划,并可以根据实际情况的变化产生修改和反馈信息。为了使MRP系统得出的物料需求计划准确有效,必须确保主生产计划在物料的采购提前期内的稳定。虽然采用看板管理的企业通常将仓库外包给供应商管理,但是仍然需要向供应商提供一个长期、叙略的物料需求计划。一般的做法是按照一年的成品俏售计划得出原材料的计划用量,同供应商签订一揽子订单,具体的需求日期和数量则完全由看板来体现。
(3)能力需求计划:MRP系统可以帮助人们把主生产计划转换为能力需求计划,生成负荷报告。然后根据负荷报告分析结果和反馈调攘主生产计划。需要注意的是在反馈调整的过程中,人工参与是很多的,现在还没有MRP系统可以自动平衡能力需求中的超负荷或负荷不足的情况。看板管理不参‘。制定主生产计划,自然也就不参与生成能力需求计划。实现看板管理的企业通过工序设计、设备布置、人员培训等手段来实现生产过程的均衡化,从而大大减少了生产过程中的能力需求不平衡的现象。看板管理可以很快地暴露出能力过剩或不足的工序或设备,然后通过不断地改进来消除问题。
(4)仓库管理:使用MRP系统的企业仓库管理的优势通常体现在两方面:一是有效地降低了库存,这是由于有了准确的物料需求计划;二是提高了库存数据的准确性,使之可以作为财务记账的可靠依据,从而提高了整体工作效率。采用看板管理后,生产线从仓库领取物料的数量被控制在看板数量之内,仓库订购的物料数量也不能超过看板数量,这样能部分地解决库存积压问题。但是由于采购的提前期不一可能一与生产线物料的需求间隔同步,又没有预先按照计划时区进行物料需求计算,在生产活动发生时通过看板传递到达仓库的物料需求能否及时得到满足就成了一个问题。仓库如果不预先准备一部分库存,那么在看板源源不断地到来时就会发生缺料情况。不进行物料需求计算,就不可能准确预计到何时发生需求,仓库的物料库存积压和短缺问题也就不可能得到完全解决。
(5)生产线在制品管理:使用MRP系统的企业在制品数量难以控制,系统中的数据与实际情况也很难保持一致。造成这一现象的间接原因是因为MRP系统是一个推进式生产管理系统,前道工序的生产是按照系统计算出的后道工序需求来确定的,而不是由实际生产过程中后道工序的需求来确定的,所以必然会出现生产线在制品管理的困难。实现准时化生产方式的企业在制品数量被控制在看板数量之内关键在于确定一个合理有效的看板数量。
(6)技术支撑:因为MRP系统在企业的计划层次运行,它是基于现有的生产情况的,所以对企业的生产设备和技术改进不提出新的要求。设备工艺落后的企业依旧一可以通过MRP系统提高整休管理水平,获得效益。有些企业忽略了看板管理的技术支撑体系,从而导致了在实践中的失败。单纯地采用看板管理不可能全而实现生产过程的合理化,应该一首先从生产过程的合理化入手,不断改进作业方法,完善生产条件,然后逐步过渡到看板管理。由此可以看出是否具备技术支撑休系是实现看板管理的关键所在。
(7)人员素质要求:MRP系统要求准确、及时地进行数据处理,人员需要经过培训使用计算机系统来取代手工作业。实施看板管理的企业不仅仅要求员工能在正常情况下进行标准化作业,还要求员工能尽快解决生产过程中的各种突发问题,保障生产流程的顺畅。总体而言,看板管理对人员素质要求高于MRP。
(8)适用行业:MRP系统适用于制造业的离散式和流程式两种生产模式,基本上各类企业都能使用MRP系统管理生产、采购、仓库、计划和则一务。准时化生产方式的适用范围就比较窄了,通常只有采用流水线方式制造或装配产品的企业才使用。典型行业是汽车制造业。但是准时化生产方式中的一些管理思想,如杜绝浪费和过量生产、柔性生产计划、设备快速调整、全员参与改善活动等等,对于所有企业都是有借鉴意义的。
2.一种结合MRP和看板管理的模式
MRP和看板管理各有所长,又各有所短。过去企业只能在两者之中选择一种作为企业的生产管理模式,不一可避免地会遇到各自的缺陷。由此可以想到:是否可以将二者结合起来,充分发挥各自的长处,避免各自的短处。
(1)MRP系统制定维护主生产计划。当前的市场环境下,企业而对不同客户的众多需求和自身的经营规划,需要一个能迅速制定、适应各方而要求、真正刊一行的主生产计划。仅仅依靠手工作业的方式进行是很难达到要求的,因此企业需要借助计算机系统来帮助制定主生产计划。现阶段能够做到这一点的只有MRP系统。
(2)MRP系统计算物料需求计划。传统的MRP系统根据上生产计划计算得出的物料需求计划不仅仅包括原材料的需求,还包括半成品的需求。但是我们知道MRP系统计算出的半成品需求一与生产现场的实际情况并不一定一致,这是造成在制品管理困难的重要原因。所以需要使MRP不进行半成品需求的计算,直接将成品的主生产计划分解为原材料的采购需求。
为了做到不进行半成品需求计算,需要在物料清单中引入虚项的概念。虚项是用来标识通常不入库或一组不可能装配在一起的零件。MRP系统不会对虚项进行需求计算,而是直接对组成虚项的原材料进行需求计算。作为虚项的半成品的生产需求将由看板来决定。
MRP系统根据产成品的土生产计划,按照物料清单进行需求分解,计算出原材料在不同计划时区内的毛需求,然后再根据现有库存和订单情况确定最终的净需求,即原材料采购计划。即使MRP系统产生的原材料净需求与实际生产过程的看板需求数量有差异,差异也不会很大,一般不可能出现缺料或积压的情况。这说明了MRP系统制定的原材料需求计划是反映了物料的实际需求情况的。如果单纯使用看板管理来确定原材料需求,那么只有在主生产计划开始实行时而不是制定时才知道原材料的需求信息。在我国目前的市场条件和交通条件下,是很难作出及时反应的。
(3)生产现场采用看板管理。生产现场的各工序生产活动的节拍是否合拍是生产控制的关键。如果采用MRP系统来管理,就会出现由MRP系统对各工序分别日达生产指令,各工序按照其指令各自开工生产。前道工序按照系统计算出的后道工序的需求进行生产活动不一定与后道工序的实际需求相吻合。这是因为,MRP的计划时区通常是以周或天为单位的,而实际上许多企业尤其是流水线生产方式的企业,各工序的加工时间是以分钟甚至秒作单位。系统的时间单位与实际的不一致,就容易造成系统的需求与实际需求之间的时间差,从而容易造成生产现场的在制品积压和生产活动的棍乱。采用看板管理就可以避免这种情况的发生。看板在生产过程中的各工序之间周转,将与取料和生产的时间、数量、品种等相关信息从生产过程的下游传递到上游,并将相对独立的工序个休结合为一个有机的整体。 |